Application for inert ceramic balls
2022-07-04
Inert ceramic alumina balls are called ceramic balls or porcelain ball, which are used as spacers before and after the catalyst layer is filled in the reaction. Inert ceramic balls are inert and will not react with materials and play a protective role. The inert ceramic ball has the characteristics of high strength, high chemical stability and thermal stability. The inert ceramic ball can resist the corrosion of acid, alkali, salt and various organic solvents. Natural gas and environmental protection industries. As the support and covering material of the catalyst in the reactor, the inert ceramic ball can buffer the impact of the liquid and gas entering the reactor on the catalyst, protect the catalyst, and improve the distribution of liquid and gas in the reactor.
Inert ceramic balls have the characteristics of high strength, high chemical stability, thermal stability, high pressure and corrosion by acid, alkali, salt and various organic solvents. In addition, activated alumina is generally not called ceramic balls, but inert alumina balls is called ceramic balls.
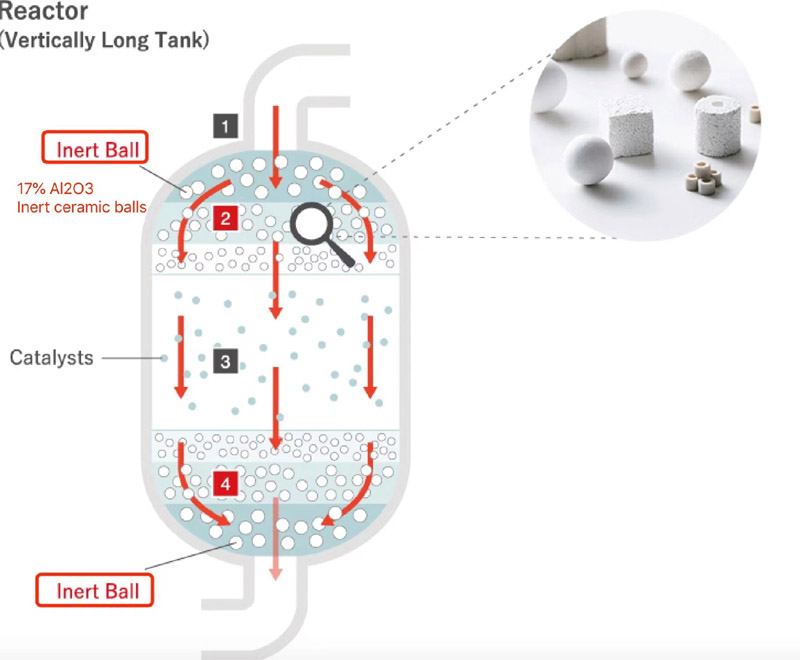
Below we’ll list some examples to explain the use of inert porcelain balls:
One. The adsorption dryer is filled with molecular sieve and activated alumina, and inert ceramic balls are added to the bottom layer
1. The main function of molecular sieve is to adsorb acetylene and carbon dioxide.
2. Activated alumina releases less latent heat when absorbing water, and absorbs water preferentially, which contributes to the subsequent adsorption effect.
3. Inert ceramic ball has good hardness and increases strength (silica gel can also be used, the purpose is the same, and it has a protective effect)
If conditions permit, we recommend filling inert alumina ceramic balls at the bottom of the adsorption tower to protect activated alumina and molecular sieves. It is also possible to pack molecular sieves in the middle and activated alumina at both ends. Of course, there have been cases if all molecular sieves are filled, but the overall cost is high. If a certain amount of inert ceramic balls are properly filled at the bottom, a certain cost can be reduced.
Two. Filling of chemical packings in hydrogen oxide (hydrogen peroxide) project
17% Al2O3 ceramic balls, the bulk density is 1300 ~ 1400kgs/m3, and the heat resistance temperature is above 1050 degrees. If the heat resistance exceeds 1350 degrees, you can choose ceramic balls with higher Al2O3 purity, such as 30%, 40%, 50%, 60% Al2O3 and high aluminum ceramic balls.
Usually in the hydrogen peroxide production process, inert ceramic balls are used at the bottom and top of the hydrogenation tower. The commonly used sizes are 13mm and 19mm, which mainly play the role of compaction, protecting and supporting activated alumina and active catalysts.
Three. Ceramic balls are also widely used in large-scale coking projects, coal chemical projects, and refining and chemical projects.
Four. 99% high alumina ceramic balls are used for heat exchange tower packing
The crush strength and temperature resistance of 99% alumina ceramic balls is much higher than 17% ceramic balls. In the heat exchanger, the role of 99% alumina balls in the tower is: As a supporting layer, the protection strength is not good. Catalyst, also known as catalyst carrier. As a medium, the high alumina ceramic ball filler can make the gas and liquid evenly turbid, increase the contact surface, and can also cause virtual heat. Because the working temperature in the exchange furnace is high, 99% ceramic balls, the higher the Al2O3 purity is, the higher the temperature resistance and the crush strength is.
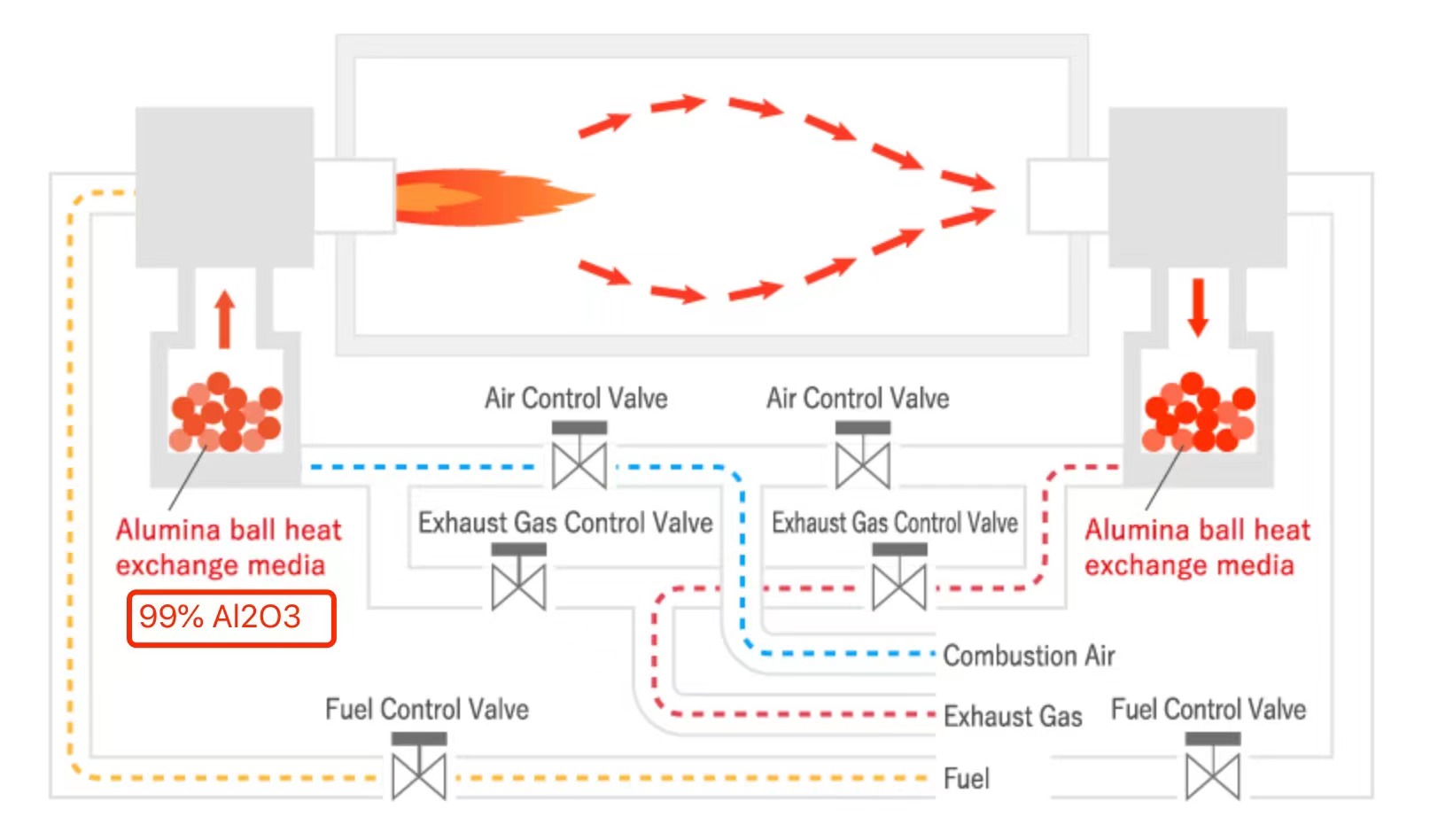
Inert alumina ceramic balls are widely used in chemical industry, petrochemical industry, gas industry, etc. Generally, the catalyst will be replaced after three years. At that time, the ceramic balls are also need to be replaced. why? Because the catalyst needs to be replaced more frequently in the heavy corrosion industry, and the ceramic ball is kept at high temperature for a long time, although the surface strength seems to be OK, in fact, its strength has become very poor. In order to prevent the ceramic balls from being broken, it is best to replace them together to avoid crushing due to insufficient strength, and bring them to the equipment below, which increases the resistance of the tower and affects production.
In many towers, the filled inert ceramic balls are located in the upper and lower parts of the tower respectively, and the main functions are also different:
1) Porcelain balls are filled in the upper part, which plays a role in distribution and impact prevention, and if there are short-term phenomena such as low temperature and liquid, it can heat up and vaporize on the ceramic balls to prevent the catalyst from being impacted.
2) Filling ceramic balls in the lower part has the effect of reducing catalyst loading and preventing small particles of catalyst from entering the downstream.
Jiangxi OIM Chemical has different type of inert ceramic balls. The ceramic balls required by different industries also have different requirements. If you have any questions about inert ceramic balls, please feel free to contact us to discuss.